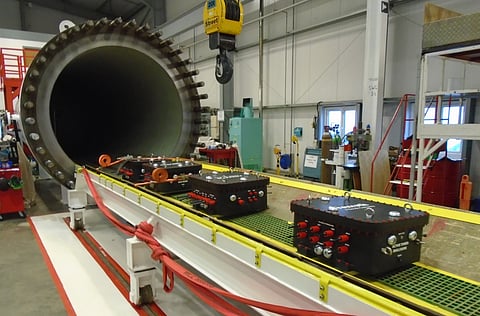
Pressure testing of safety critical subsea equipment is a crucial stage in any operation to ensure that vehicles, and their supporting technology, can withstand the high pressures and extended submersions of the subsea environment.
Forum Energy Technologies (FET) currently hosts one of the largest horizontal hyperbaric testing facilities in Europe. The facility is widely used by a number of industries including oil and gas, defence, the scientific community, telecommunications, and many other sectors that are developing and manufacturing subsea equipment. The FET Test Facility provides the opportunity for subsea equipment developers and manufacturers to have their products pre-qualified without the requirement for costly and time intensive sea tests.
The premises hosts a full range of testing capabilities with multiple chambers, a test pool, and a team of experts ready to assist, delivering increased project efficiency and reducing timeframes. The range of services offered includes hyperbaric, hydrostatic, endurance, flushing, product qualification and verification, and bespoke testing services.
With the ability to cater for all types of testing, whether it is hyperbaric or hydrostatic, the company has the in-house capabilities and equipment at its facility in Kirkbymoorside, UK to accommodate clients' needs. FET's Test Facility operates eight pressure vessels of different sizes and specifications available that can be used for various types of testing with water, oil, or gas. FET can also provide live testing of the electrical or hydraulic functions within the pressure vessels.
Upgraded testing tanks, 20 tonnes safe working load lifting cranes, experienced personnel and detailed procedures are in place offering independent testing for all types of subsea, defence and oceanography equipment, following the client's test specification.
The largest testing vessel measures 2.3 m diameter x 8.1 m length and is rated to 3,500 psi (241 bar), allowing operators to assess equipment at the high pressures encountered during subsea operations. It has a maximum load capacity of 70-tonnes, including the weight of water, and holds approximately 43m3 of water. Installed with a HMG300 Hydac system, the vessel can also accurately and efficiently capture data, including pressure, temperature, and flow throughout assessment to provide precise operational updates.
For assessments, the large chamber is pressurised using an electrically driven water pump which can pressurise to a maximum rate of 58 psi per minute. There are a maximum of 22 penetrations for electrical, hydraulic, pneumatic, and instrumentation.
The horizontal loading system simplifies the installation and hook-up of test equipment, and a 20-tonne overhead crane is also on-site to assist with heavy equipment testing. The hydrostatic pressure test vessel is fitted with a detachable semi-ellipsoidal end cap for easy loading of components. All testing is carried out to the highest standards and in compliance with Health and Safety Executive Guidance GS4 Standard.
For hydrostatic testing, the vessel features a secure area in which internal assessing can be carried out for various items such as electrical cables and boards, manifolds, function of manipulators, torque tools, submarine hulls, camera and light encased equipment, hot stabs and receptacle, gas cylinders and emergency life support store pods, amongst others. This also allows for pressure testing up to 30,000psi.
In addition to the hydrostatic pressure test centre, FET's facility hosts a 6m deep tank available for wet commissioning or full-scale interface tests. Measuring 9m wide x 11m length the tank is ideally suited to enable ROV and ancillary testing.
FET has a dedicated engineering team and technicians based at the premises to assist in testing operations. Recent upgrades mean that tests can be done 35 per cent faster than previously.
Improvements include enhanced pumps, which can reduce tank filling by 45 minutes. The tank's door, which is fitted on train tracks and is pulled in using a winch, has also been upgraded with the latest technology, allowing it to be opened and closed 1.5 hours quicker than before.
The company's testing capabilities also proved crucial for the deployment of its most sophisticated Submarine Rescue Vehicle (SRV) to date – LR11.
Characterised by a robust design, and incorporating all the newest technologies available, LR11 was developed to become the world's most advanced rescue submersible. Built for a foreign navy in the Asia-Pacific region, the SRV is the latest built by FET following the success of previously delivered systems including NATO Submarine Rescue System (NSRS), which entered service in 2008 and "remains the benchmark", according to many of the pilots in the industry.
SRVs manufactured by the company are typically designed to operate throughout the world at 500 metres to 650 metres water depth. This is not a limitation of the technologies but constrained by the operating/crush depths of the distressed submarines. FET's experienced personnel can supply a craft to operate at any depth required, with vast experience of supplying ROVs where typical depths are 4,000 metres and above.
Following approved engineering procedures, the internal and external testing of the SRV required two months of preparation before the vessel was brought to the company's Kirkbymoorside premises. The main challenge of testing such a large vessel was ensuring it could safely fit inside the testing tank due to its size.
FET's in house welding and fabrication capabilities, as well as its state-of-the-art electronics lab, mean that the company can be a one-stop-shop for equipment testing, handling the procedure from start to finish.
Generally, pressure testing is done at one and a half times the technology's working pressure. For example, the SRV was tested at 76 bar, which replicates 760 metres.
Due to the safety critical requirement of SRVs, power conservation and redundancy were primary considerations during the engineering phase. A number of advanced technologies and systems were incorporated to conserve power and provide back-up in the event of a failure. All these systems were operated under pressure as part of the SRV's testing, with under pressure function testing of electric, mechanical, and hydraulic equipment all being part of the company's capabilities.
With the defence sector continuing to realise the benefits of highly advanced vehicles and equipment that support their operations, this will place greater demand on subsea testing facilities. It's vital that defence assets can be accurately and efficiently tested in dedicated premises to ensure the integrity and performance of such equipment. Facilities such as FET's hyperbaric vessel can support global defence activity in this regard.