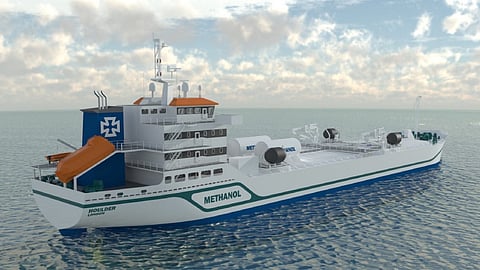
UK-based design and engineering consultancy Houlder has unveiled concept design images of a new methanol bunkering vessel with a cargo capacity of 10,000 cubic metres. The vessel is being developed by Houlder as part of the SPINE Project, which project aims to establish an interface between ships, remote control centres, port operating systems, and national energy infrastructure to address challenges in maritime decarbonisation and autonomy.
The methanol bunkering vessel design includes semi-automated crane systems for supplying methanol to other ships of a wide size range, including cruise ships and large container vessels. Houlder worked to optimise the vessel's layout for maximum efficiency and compliance.
The use of methanol as both cargo and fuel presented unique spatial considerations, given its lower density compared to conventional fuels, the different regulatory requirements concerning storage and use as cargo or fuel, and associated handling spaces. Houlder's design team explored allocated space within the hull to balance these requirements within a vessel that is of comparable size to existing small tankers, while adhering to strict safety regulations.
Houlder said the placement options for propulsion fuel tanks and other critical spaces were thoroughly reviewed to ensure operational effectiveness without compromising safety, performance, and vessel size. Electric powertrain architecture was also incorporated, allowing for future upgrades to fuel cell technology, and providing environmental benefits with respect to reduced noise.
To optimise vessel efficiency, Houlder utilised the latest digital twin technology to create a virtual world. This was used to analyse adjustments to existing ship operations, to design brand new vessels, or to outline various ways to save fuel and cut associated GHG emissions on specific voyages or across all operations. Innovative CFD was deployed within this process to consider various solutions such as twin propeller configurations and bulbous bow designs.
The impact of a minimal ballast philosophy on the design was also assessed – the propeller size and subsequent propulsive power requirements, for example. These allowed Houlder to analyse the trade-off between propeller size and number against fuel efficiency in both full load and ballast conditions across a range of different operating profiles. As a result, numerous design variants exist, ready to be optimally balanced for OPEX and CAPEX for particular operating routes, and taking owner preferences into account.