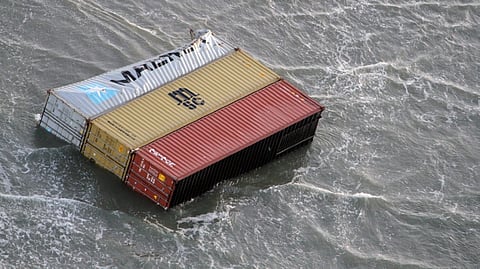
More than 80 per cent of goods traded worldwide travel on one of the more than 90,000 cargo vessels plying the world's oceans. At the heart of it all is the freight container, one of the most important inventions for global trade.
Little did we know when freight containers first came into being back in the 1960s just how widespread they would become in cargo operations. In 2019, the international liner shipping industry transported approximately 226 million containers, with cargo transported valued at more than US$4 trillion.
The first truly successful container shipping company dates to 1956, when American trucking entrepreneur McLean put 58 trailer vans, later called containers, aboard a refitted tanker ship, Ideal X, sailing them from Newark, New Jersey to Houston, Texas.
However, the first truly international transport of containers was by Atlantic Container Line, which was formed in 1965 by a consortium of four shipping companies: Wallenius Lines, Swedish America Line, the Transatlantic Steamship Company and Holland America Line. These were joined by Cunard and CGT in 1967.
The initial reason for implementing container carriage was to reduce the high rates of pilferage and damage to general cargo. However, the other advantages of shipping freight in containers were soon found to be:
It was about this time that I was serving as an apprenticed marine engineer aboard Cunard cargo vessels on the transatlantic route from Liverpool. Whilst in New York on one trip we were having a beer in the ward room with the stevedore foreman who was asked how containerisation would affect him. "What the hell, we'll just take a whole container!" he responded.
Cargo theft is seen by the perpetrators as a low-risk, high-reward crime carrying minor criminal penalties. The FBI reports that less than 20 per cent of stolen cargo is ever recovered.
During the 1990s there was a proliferation of container thefts in southern Chinese ports. Thugs would regularly board container vessels with bolt-cutters and, clearly having inside information, open selected containers to steal any valuable contents.
Cargo is also lost when a container is lost at sea. During a twelve-year period (2008-2019), the World Shipping Council has estimated that there were on average a total of 1,382 containers lost at sea each year. Thankfully, the trend is downwards.
Losses may be caused by fires and explosions that can happen both on deck and underdeck. The rules state that dangerous cargoes (DG) should be stowed on deck, usually outboard near the bow flare. This is so that they can be easily jettisoned.
However, DG containers are often mis-declared and stowed underdeck. This can result in catastrophic consequences, the Hyundai Fortune fire and explosion being a classic example.
Losses of deck stowed containers due to freak waves and parametric rolling are becoming more frequent.
Freak or rogue waves are just that – unpredictable and spasmodic. Meteorologists and oceanographers have been unable to find any patterns. Rogues, called "extreme storm waves" by scientists, are those waves that are greater than twice the size of surrounding waves being very unpredictable and often coming unexpectedly from directions other than prevailing wind and waves.
Parametric rolling is an unstable phenomenon that can quickly generate large roll angles coupled with significant pitch motions. The rolling occurs in phase with pitch, and on containerships introduces high loads in the containers and their lashing systems. It appears that post-Panamax containerships may be particularly prone to this behaviour. This is an important issue considering the large number of these vessels scheduled for delivery in the next few years.
Parametric rolling is experienced only on container ships. It occurs when natural roll period is between 1.8 to 2.1 times the encounter period, normally associated with the pitching period. The larger the flare the more likely is the parametric roll angle and wider range of resonance. It requires a group of waves above a threshold or critical height for parametric roll to be initiated and sustained; the threshold depends on size and shape of the hull.
The size of container ships is still increasing. The new container ships coming into service have large bow flare and wide beam to decrease the frictional resistance generated when the ship fore end passes through the water. As a wave crest travels along the hull, it results in flare immersion in the wave crest and the bow comes down.
The stability (GM) varies as a result of pitching and rolling of the ship. The combination of buoyancy and wave excitation forces creates rapid rolling with larger than normal rolling angles with resultant increased and excessive rolling loads on the containers.
Container stacks that have not been stowed in an appropriate manner on deck will increase the loads on stacking cones and twistlocks, particularly when heavier loads are stowed higher in the stack where the accelerating forces are also higher. This is evidenced by the base cone pieces failing whilst the container twistlocks remain in place. Poor stowage and misdeclaration of container contents weights exacerbate this situation.
When vessels are built or modified their container lashing plan must be approved and endorsed by Class. Class carries out calculations where the worst possible conditions are used to find the maximum loading on lashings. If they are within limits, the lashing plan is approved. When container lashings fail, marine consultants use similar calculations to find the loads in the lashings.
Actual conditions experienced by the vessel when the lashings failed are entered into the calculations. The results show where the loads in lashings exceed Class limits.
If the stability of the vessel is correct there should be no lashing failures. However, lashing failures are also common on the smaller container feeder trades. One of the most common causes is poor stability where the vessel is too stiff with a large GM. This is caused by the crew failing to deballast tanks for a loaded passage. Losses also tend to be more attributable to human error, for example:
The containers lost overboard will usually sink very quickly. However, those that have lighter cargoes may float just below the sea surface, presenting a navigational hazard. There are many cases of smaller vessels' hulls being holed by contact with floating containers. Insurance losses are therefore significantly increased by the loss of the containers and damage to other vessels.
Nobody could have foreseen the hazards now facing the container shipping industry back in the 1960s. As these hazards are becoming more frequent perhaps it is time for a rethink and assessment of current lashing arrangements. Recommendations have been made by various organisations with a stake. These include:
Most major catastrophes can be shown to be caused by a number of smaller problems contributing to the final event with the possible loss of a ship, its cargo and crew. A misdeclared dangerous goods cargo in a container stowed below deck has been shown to be a classic case. A well-publicised prosecution of those responsible would go a long way to reducing such incidents.