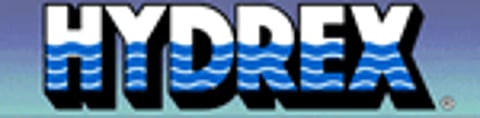
When one of the four 40-tonne swing-up azimuth thrusters of an offshore crane barge which was servicing rigs on an oil field off the coast of Gabon malfunctioned, Hydrex was called in to remove the thruster and perform the necessary repair work while the unit stayed at anchorage just outside the field.
While it is possible to maintain position with three thrusters, the fourth needed to be repaired straight away. This had to be done in the short timeframe between two scheduled operations. The barge could only leave the oil field in this period and all repairs and other servicing work needed to be carried out before the start of the next operation.
A similar operation had been planned and carried out by Hydrex three years ago. Just as with the recent operation, going to drydock was not an option as the nearest suitable location was South Africa and this would have taken the repairs far beyond the available time frame.
For this reason a large mobdock (measuring 9 x 6 x 2 metres and weighing over 25 tonnes) was constructed under Hydrex supervision in Belgium after which it was transported to Gabon.
There it was stored after the repair to be used at short notice whenever future repairs were required on the thrusters. This allowed for a very fast mobilisation and execution of the operation which was carried out last month.
First an operations base was set up on a work barge next to the crane barge. The mobdock was then installed and all water was pumped out of it to create a dry working environment underwater. The water sensitive parts of the thruster were then sealed off after which the mobdock was removed. The thruster unit was lowered onto a special support unit under the barge and brought to the work barge.
Subsequently Hydrex engineers dismantled the thruster under the supervision of a representative of the manufacturer. The entire gearing was taken out, thoroughly checked, cleaned and reinstalled. The thruster's propeller was disconnected in its entirety and replaced by the propeller of a spare thruster that had also been brought onto the barge.
The spare thruster (together with the old propeller) was then brought ashore for transportation to the workshop where it will be overhauled. Once it is returned the owners will have a fully operational thruster ready to be installed if another breakdown occures.
Meanwhile the fully checked original thruster with its new propeller was reinstalled into the crane barge following the reverse procedure.
Finally commissioning and testing was carried out satisfactorily. The offshore unit was fully operational again, well before the start of its next operation. This presented a major saving in time and money for the owner as the offshore unit did not have to go off hire to be taken to drydock.
It was an extremely precise operation requiring a great deal of coordination and organisation to ensure that all went smoothly. There were detailed safety and technical procedures that had to be met in order to access the thruster from within the engine room as the thruster was located outside the vessel under the water line. Despite this, all technical work was performed smoothly by qualified Hydrex diver-technicians. They worked in shifts to finish the operation as soon as possible and without any loss of quality.
For further information contact: