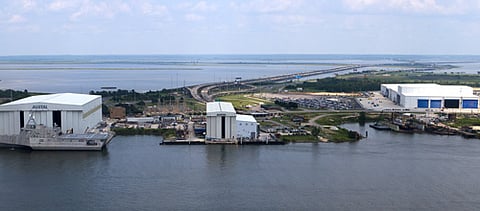
Australian aluminium shipbuilder Austal has declared that by 2013, when it will be operating at maximum efficiency, its Module Manufacturing Facility (MMF) in Alabama in the United States will have the capability to deliver two 103-metre Joint High Speed Vessels (JHSV) and two 127-metre Littoral Combat Ships (LCS) each year.
The shipyard started operations with the construction in 2000 of two 45-metre offshore support vessels. Beginning in 1999 with a single construction bay and fewer than 100 workers, Austal USA is now the largest manufacturing company in Mobile, Alabama.
In 2005, facing the challenge of producing multiple orders of large complex vessels for the US Navy's transformational fleet programs, Austal USA embarked on a development plan to expand its production capability and improve its productivity and efficiency.
Starting with visits to leading shipyards in the US, Korea, Australia and Germany, and working with industry experts in shipbuilding and manufacturing, the company worked to combine Austal's three-dimensional design and modular construction processes with a Module Manufacturing Facility.
Austal USA uses a three-dimensional design process that divides construction into modules, which are constructed on a production line entirely undercover. Uncut metal enters at one end of the production line and modules, approximately 85 percent complete, emerge at the other end ready to be assembled in one of two large vessel assembly bays.
Aluminium plate and extrusions enter at the eastern end of the building where two computer-controlled routers cut the metal into the required shapes. The cut metal then moves through the module assembly area, the first phase of the production line, a series of work stations where stiffeners and frames are joined together and the modules take shape on trolleys that move the increasingly complex modules from one station to the next. A network of overhead gantry cranes is used to lift materials and equipment into position in each module.
Modules that require more than a week in this stage of the production process, such as a complex wheelhouse, can be broken out of the line to a separate part of the facility where work can progress without holding up production of following modules.
Normal modules move to the outfitting phase of the production line where workstations manufacture and install pipes and small components as well as air-conditioning, electrical and engineering machinery and equipment.
Once the modules emerge from the MMF they are transported to the vessel assembly bays using multi-axle transporters capable of lifting modules weighing over 400 tonnes.
Austal USA's investment in the MMF alone totals approximately US$85 million and is already paying big dividends with experience in both the LCS and JHSV construction programs confirming productivity improvements of 30 percent in fabrication and 40 percent in outfitting in just one year.
With the first Austal-built LCS, 'USS Independence' (LCS 2), now in service, the second, 'Coronado' (LCS 4), heading for completion in late 2012 and construction of the first 103-meter JHSV for the U.S. Army underway, Austal USA is awaiting news in August 2010 of whether its bid to construct the next ten LCSs will be successful. Should Austal USA prevail its workforce could grow from 1,600 to 3,500 people.
Disclosure: Members of the Baird family or companies in the Baird Publications group own shares in Austal.
For further information contact:
{WISroYQ symbol='ASB.AX'}