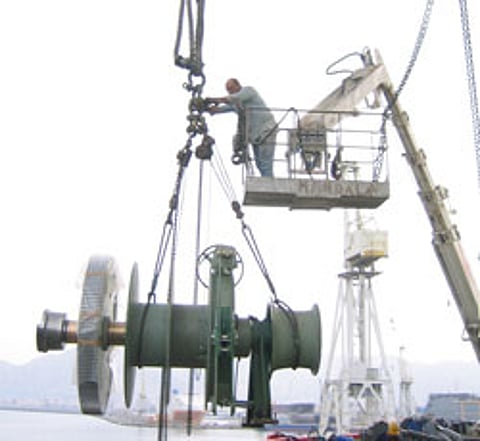
A new task-force-service department of the Uetersen Maschinenfabrik Hatlapa has been introduced to decrease re-equipment and installation time as well as increase flexibility in delivering marine equipment.
Since new vessel orders are declining due to the economic downturn, services, repairs, alterations and spare parts delivery are of growing importance in the marine industry. The first point of contact at Hatlapa when a vessel needs assistance is the marine engineers. This improves response time, which is a critical factor.
For instance, a German containership had a collision in the North Sea, colliding with a much larger vessel, and the steering gear had been damaged. The collision had been so severe that the 260-metre long container had a leak measuring the height of the port-side engine room. As water continued to run through the leak, the vessel was towed to shallower waters in order to prevent the ship from sinking. Three of the 900 containers went overboard, and the crew suffered from smoke inhalation and had to seek medical assistance.
Both of the combined anchor and mooring winches in the ship's bow had been completely damaged in the accident and had to be replaced, and the vessel had to go through a complete overhaul. The ship owner had originally been told that the delivery time for the replacement winches was six months.
However, the Hamburger ship owner did not want to wait that long and started making phone call to different companies selling deck machinery. Opitz received all of the data of the damaged machinery via email and discussed with the different departments within Hatlapa how they could provide a solution to the dilemma.
The specialist winches that the damaged vessel had had on board were no longer in stock, but it was possible to gain the four much needed winches from another customer's order and assemble them so that they made up the two specialist winches, that matched the specification of the winches from the damaged vessel. "Make two into four –a lucky streak and challenge at the same time", was what Opitz was able to tell the ship owner on the same day. A particular challenge, as the chain sprockets had to be manufactured in house, due to very long lead times. Hatlapa was then asked to put together a formal quotation for the delivery and fitting of the ordered machinery. Opitz spoke to all departments involved to start the quoting process and had an estimate ready the very next day: with a lead time of nine weeks for delivery and installation of the machinery. However, this was still too long –wasn't there any way to make it happen faster, enquired the ship owner.
This is when the Task Force Service team stepped in. The group was created three years ago for cases just like this. Within this group, department managers from engineering, purchasing, service, sales and production are involved. The group of specialists investigated how to shorten the lead-time. "We have come to the conclusion that in special cases like this, with considerable effort, the lead time could be reduced to seven weeks", recalls Opitz. This included shift work and overtime on weekends. The ship owner was delighted, and approved the order only 16 days after the collision.
Six weeks later, a week earlier than discussed, the specialist job was delivered from Uetersen to the repairs shipyard in Hamburg and two weeks later the unlucky vessel was already back in the water – not even three months after the collision. In only eight weeks the multipurpose vessel had been restored to its original condition.