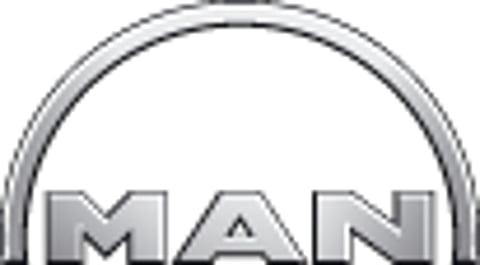
MAN Diesel and Turbo has unveiled two-stage turbocharging to the market with the introduction of its TCX generation.
Two-stage turbocharging enables the charge-air pressure to be increased substantially while simultaneously reducing exhaust emissions, despite the increased specific engine output.
Two-stage turbocharging systems consist of two turbochargers of different size connected in series. The exhaust gas coming from the engine drives the turbine of the smaller, high-pressure turbocharger (the first stage), which in turn drives the turbine of the larger, low-pressure turbocharger (the second stage).
The low-pressure turbocharger's compressor draws in ambient air and sends it via an intermediate cooler to the high-pressure turbocharger's compressor. Here, the air is compressed once again and, via a further charge-air cooler, sent to the engine.
The system adapts to varying operating conditions either through controlled turbine bypass or by variable nozzle rings (VTA). Two-stage compressors also have bypasses designed to suppress compressor surging.
With the new TCX Series, MAN Diesel and Turbo has developed a new generation of turbochargers especially aimed at two-stage turbocharging. The TCX series is based on the design philosophy of the TCA/TCR series with uncooled casings and durable plain bearings.
While the TCA/TCR series use axial and radial turbines respectively, the new TCX-series employs a diagonal turbine that is suited to the lower-pressure ratios.
The lower-pressure ratios affect flow-ducting components as well as bearings and casings. Especially at the high-pressure level, increased thrust forces are imposed on the bearing system. Also the sealing air used for turbine shaft sealing is adjusted to suit the changed pressure levels.
Furthermore, the tightness of all turbocharger casings must be ensured because of the higher pressures in the higher-pressure turbocharging stage.
For further information contact: